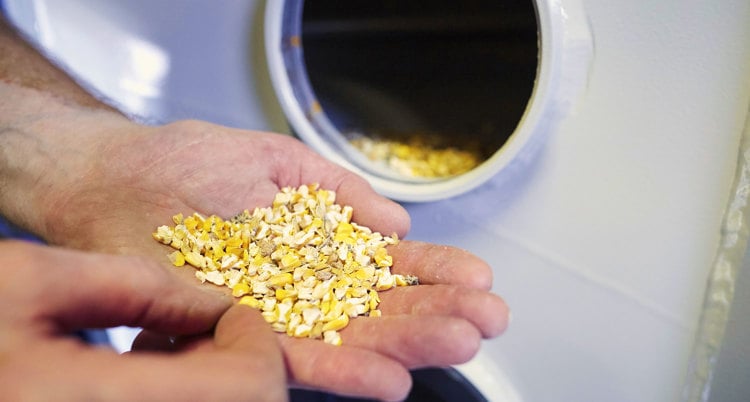
Durante esse processo, os ingredientes são reduzidos em seu tamanho através de forças de impacto, corte ou atrito. Os objetivos básicos da moagem são:
- Uniformizar os tamanhos das partículas, facilitando o processo de mistura e reduzindo o potencial de “desmistura” da ração durante os processos posteriores;
- Adequar o tamanho das partículas para atender e/ou favorecer o consumo do alimento e os processos de digestão (a amplitude da granulometria dependerá da espécie para a qual a ração produzida será destinada e fase/idade do animal);
- Auxiliar no processo de peletização através da adequação da granulometria da ração visando o aumento da superfície de contato, favorecendo a ação do vapor e alcançando uma melhor gelatinização, e consequentemente, a melhoria da qualidade do pellet. Além disso, a correta granulometria evita a presença de partículas grosseiras no pellet agindo como pontos de fissuras.
A moagem é um processo-chave dentro da fábrica de ração. Se pelo ponto de vista nutricional, partículas pequenas tem maior superfície de contato para ação dos sucos digestivos, favorecendo a digestão, pela perspectiva da produção, quanto mais grosseiras forem as partículas menores serão os gastos com energia elétrica e maior será a eficiência de produção (toneladas/hora). Portanto, o controle desse processo e equilíbrio entre os parâmetros de qualidade, produtividade e eficiência energética, são fundamentais para a rotina fabril e sucesso de suas operações.
De acordo com Klein (1999) devemos nos atentar a alguns pontos críticos no processo de moagem:
- Capacidade dos moinhos: pode se tornar o gargalo da produção. Para atender à demanda por grandes volumes, são deixados de lado importantes parâmetros de qualidade;
- Limpeza e desinfecção: como qualquer outro componente da fábrica, os elementos de moagem também precisam ser limpos e desinfetados periodicamente;
- Controle do DGM (Diâmetro Geométrico Médio) e do DPG (Desvio Padrão Geométrico): atender às necessidades de acordo com a espécie e fase de criação;
- Processo de exaustão/aspiração: melhora a produtividade da moagem, auxilia no resfriamento do produto evitando, assim, o superaquecimento do ingrediente, o que leva a perdas nutricionais e possível condensação nos silos e transportadores, comprometendo a condição microbiológica da fábrica. Desse modo, é essencial realizar o controle da temperatura do produto moído, que não deve ultrapassar 8°C a mais em relação a sua temperatura de entrada na etapa da moagem;
- Umidade do ingrediente: quanto maior a umidade do produto a ser moído maior será a perda de água durante o processo, o que aumenta as chances de condensação, sendo que esta, está diretamente relacionada ao gasto energético do processo. De maneira geral, considera-se o aumento de 7% no consumo de energia para cada 1% a mais de umidade constatada no ingrediente moído.
Tipos de moagem
Existem basicamente dois conceitos possíveis: a pré-moagem ou a pós-moagem – também chamada de moagem conjunta.
Essa definição é fundamental, pois o modelo impactará em toda diagramação da fábrica e no custo final do projeto.
- Pré-moagem: nesse modelo de moagem, os ingredientes são moídos individualmente, armazenados em tanques de dosagem e posteriormente dosados. Para as dietas brasileiras, resumidamente devem ser moídos o milho, algum outro grão alternativo e o farelo de soja. Considerando essa característica inerente às dietas brasileiras, com reduzido número de componentes a serem moídos, esse é o modelo originalmente trabalhado nas fábricas do país. A pré-moagem apresenta dois pontos bastante positivos: o processo de moagem atua de forma independente da linha de mistura, o que maximiza o uso dos moinhos, permitindo a continuidade do processo em caso de parada da moagem – dependendo do pulmão dos produtos moídos, logicamente. Outro ponto positivo é a possibilidade de se trabalhar com diferentes granulometrias para cada tipo de ingrediente. Como pontos negativos temos o elevado investimento em silos e transportadores adicionais e a dificuldade de moagem de alimentos fibrosos de forma individual;
- Pós-moagem ou moagem conjunta: de acordo com Lara (2010) a adoção do modelo teve início, no Brasil, em meados dos anos 90 por influência do modelo europeu de produção de ração. Em linhas de produção com moagem conjunta, os moinhos ficam entre o sistema de dosagem e mistura, cujos ingredientes são dosados diretamente dos silos de armazenamento antes de serem moídos. Esse sistema atende melhor às condições de uso de uma grande variedade de ingredientes que necessitem de moagem – como é o caso das dietas europeias. Como vantagem deste tipo de moagem, temos o menor custo de investimento em silos e transportadores; melhor uniformidade da granulometria da ração e maior facilidade para moer ingredientes de difícil moagem por estarem misturados a outros de maior facilidade. A grande desvantagem desse sistema é o fato de ser ligado a mesma linha de produção que a mistura, portanto, a capacidade da linha principal mantém-se limitada à capacidade de moagem. Com relação à capacidade dos moinhos, esta não é completamente utilizada, uma vez que permanecem vazios nos intervalos entre as bateladas.
Equipamento chave: moinho
Para o processo de moagem, o equipamento mais utilizado mundialmente é o moinho de martelo. A moagem ocorre pelo impacto dos martelos em alta rotação sobre os produtos. O controle do tamanho das partículas se dá, principalmente, pelo diâmetro dos furos contidos nas peneiras do moinho. Apesar de parecer simples, na prática são observadas múltiplas variações de respostas à granulometria frente aos equipamentos utilizados. Na maioria dos casos, o operador tenta controlar a granulometria dos produtos alterando apenas o tamanho dos furos das peneiras – muitas vezes sem sucesso no resultado. Apesar do diâmetro do furo da peneira ser o principal agente definidor da granulometria, outros parâmetros são importantes e contribuem ativamente sobre o controle do DGM do ingrediente ou da ração final. De acordo com Lara (2010), outros fatores importantes que estão diretamente envolvidos no processo de moagem são:
- Velocidade periférica: geralmente a velocidade periférica de trabalho dos moinhos de martelo para dietas de aves é de aproximadamente 90 m/s. Velocidades superiores reduzem o tempo que as partículas têm para deixar a câmara de moagem e nesse caso, partículas que já estiverem com tamanho adequado terão maior chance de sofrer nova quebra. De forma geral, podemos concluir que velocidades periféricas elevadas tendem a gerar granulometrias mais finas, resultando na maior quantidade de finos na ração e consumo de energia elétrica;
- Martelos: a eficiência da moagem está diretamente relacionada com o número, espessura e desgaste dos martelos. Quanto maior o número de martelos maior a probabilidade de encontros subsequentes com a partícula, contribuindo para uma moagem mais fina. Para dietas de aves com granulometria mais grosseira, a redução do número de martelos é uma alternativa a ser considerada, com o intuito de favorecer a granulação mais grosseira, reduzindo, assim, o consumo de energia. Isso ocorre, pois a pressão do impacto advinda dos martelos finos é maior devido à aplicação da força em uma área de contato menor. Martelos grossos tendem a empurrar mais as partículas. O desgaste dos martelos precisa ser supervisionado periodicamente, com o objetivo de evitar o superaquecimento do produto, perda de produtividade e maior risco de rompimento da peneira.
- Características da peneira: o diâmetro do furo, a espessura e a área aberta da peneira impactam diretamente o processo de moagem. Normalmente, as peneiras utilizadas em dietas de aves e suínos apresentam furos entre 2,5 e 5 mm, tendo relação direta sobre a granulometria desejada, ou seja, utiliza-se maiores diâmetros para maiores granulometrias. A espessura da peneira deve variar de 2 a 3 mm, quanto maior for a espessura, o atrito gerado para a passagem das partículas também aumenta, sendo mais eficiente para rações iniciais. Sobre a área aberta, quanto maior, aumenta-se a probabilidade de que partículas de tamanho correto deixem a câmara de moagem, elevando a produção e levando à redução do consumo de energia. O efeito negativo da menor espessura associada a maior área aberta, consiste na resistência da peneira, que por sua vez, será reduzida.
- Exaustão/aspiração: o fluxo de ar através da câmara de moagem facilita a passagem das partículas com tamanho adequado pela peneira, evitando a redução adicional desnecessária e formação de finos em excesso, diminuindo as chances de desgaste dos componentes de moagem.
Importância da granulometria em dietas para aves de produção
As aves apresentam peculiaridades em seu sistema digestório que requerem adaptações nas características físicas das rações. Dentre essas peculiaridades, a presença do bico e moela no lugar da boca e dentes, alteram todo o processo de apreensão e trituração do alimento, impactando diretamente o consumo e a dinâmica da digestão. As aves respondem de forma irrelevante ao consumo quando estimuladas através do cheiro e sabor, se mostrando mais eficientes a estímulos pela cor e tamanho dos alimentos (OLIVEIRA, 2020). Os bicos das aves são dotados de mecanorreceptores, o que faz com que haja uma resposta ao estímulo pelo contato. Nesse contexto, dietas mais grosseiras – logicamente que dentro de um limite aceitável para evitar a seleção demasiada dos componentes da ração – atendem melhor às necessidades das aves.
Dietas muito finas e com baixo DGM, dificultam a apreensão e deglutição, impactando negativamente o consumo de ração devido ao maior acúmulo de ração no bico, o que pode ocasionar lesões orais, facilmente confundidas com quadros de contaminação por tricotecenos.
Outro fator de impacto relacionado às baixas granulometrias da ração é o efeito sobre a digestibilidade da dieta. De forma geral, é valido para outras espécies que quanto mais finas as partículas alimentares maior a superfície de contato relativa, resultando em uma melhor ação dos sucos digestivos, o que consequentemente, melhora a digestibilidade da dieta. Porém, para aves adaptadas com a moela e peristaltismo reverso, partículas finas exigem menores atividades desta, elevando a velocidade de passagem do alimento. Esse efeito impacta negativamente a fisiologia da digestão das aves em diversos aspectos. Entre os mais importantes podemos citar:
- Baixa atividade da moela: a moela é um órgão muscular que depende de atividade para se desenvolver, portanto, o emprego de dietas com baixa granulometria implica em uma menor atividade e, consequentemente, gera menor estímulo para o desenvolvimento do sistema digestório, principalmente da moela, o que afeta simultânea e negativamente o peristaltismo reverso, impactando a eficiência da digestão e a homeostase fisiológica e microbiológica de todo o intestino;
- Aumento da taxa de passagem do alimento: este fator leva à implicação direta da digestibilidade do quimo, havendo menor duração da ação dos sucos digestivos, o que afeta negativamente a digestão, acarretando aumento da conversão alimentar e redução do ganho de peso. Além disso, a presença de alimento mal digerido na porção final do intestino é substrato para proliferação indesejada de microrganismos maléficos, ocasionando disbioses que podem evoluir para quadros de enterite necrótica, comprometendo a saúde intestinal das aves.
Recomendação de granulometria da ração para frangos de corte e galinhas de postura
Abaixo, você poderá conferir os parâmetros de DGM indicados pela De Heus para frangos de corte e galinhas de postura, considerando o emprego de dietas fareladas. Lembrando que, acompanhando o DGM, o indicador de uniformidade da granulometria, o DPG, deve ser sempre avaliado conjuntamente, respeitando-se o padrão com limite máximo de 2 pontos.
Preocupados em garantir maiores ganhos em eficiência alimentar e produtividade, estamos sempre buscando investir em novas tecnologias e nos melhores equipamentos com o objetivo de assegurar o adequado controle e gerenciamento de nossos processos fabris.
De Heus, segurança e qualidade como referência.
Referências bibliográficas
Lara, M. Processo de produção de ração – Moagem (parte 1). Revista Engormix. 2010. Disponível em https://pt.engormix.com/avicultura/artigos/producao-de-racao-t36941.htm.
Klein, A. A. Pontos críticos do controle de qualidade em fábricas de ração – uma abordagem prática. Anais... I Simpósio Internacional ACAV – EMBRAPA. Concórdia,1999.
Existe algum desafio em que podemos ajudá-lo?